Les données énergétiques, une mine d’or à surveiller et exploiter
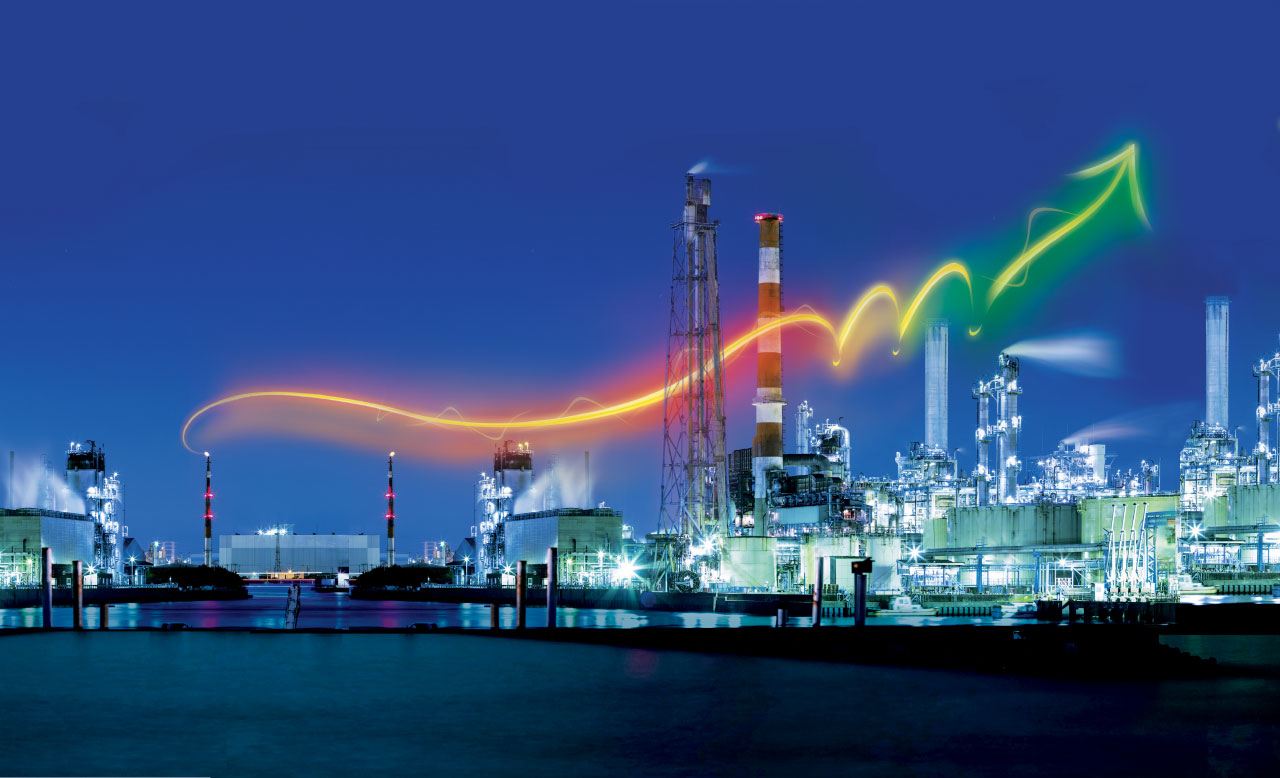
Réduire sa facture énergétique commence par avoir une bonne connaissance de ses consommations. Si les audits et l’instrumentation satisfont une partie des besoins, les outils de monitoring et SIGE contribuent à l’analyse des données recueillies afin de mettre en place des actions d’amélioration pertinentes.
Mesurer la consommation énergétique de son usine offre la possibilité d’établir des diagnostics de consommation et de mettre en place des plans d’action afin de la réduire. En ligne de mire pour l’industriel : plus de compétitivité ainsi qu’une réponse aux obligations réglementaires et enjeux environnementaux.
Le secteur industriel pourrait réaliser 20% d’économie d’energies d’ici 2030 d’après l’Ademe (Agence de l’Environnement et de la Maîtrise de l’Énergie)
Monitoring, sige : quelles différences ?
Le monitoring des installations industrielles permet de relever des informations afin d’aider par exemple à conduire une ligne de production. Il n’est pas nécessairement dédié à la mesure de données énergétiques.
Le SIGE (Système d’Information et de Gestion Energétique) est quant à lui plus complet et donne une vue globale de la consommation énergétique à des endroits spécifiques. Robin Cochard, assistant responsable d’affaires chez Actemium Maisons-Laffittes, précise : « Il est composé de 3 briques élémentaires : les dispositifs de mesure, les moyens de relève et les moyens d’analyse ». Juliane Jundt, Energy Efficiency Engineer chez Actemium, poursuit : « Il englobe toute la chaîne de valeur du monitoring, de la mise en place de capteurs à la remontée des données en temps réel, leur analyse et visualisation ». Il permet par exemple de comparer des lignes de production, des usines, des modes de conduite du process…
En identifiant et quantifiant l’énergie consommée dans les process en temps réel, un SIGE contribue à définir un potentiel d’économie et à améliorer le rendement énergétique. « Le logiciel utilisé par le SIGE permet aux collaborateurs de planifier, prendre des décisions et mettre en œuvre des mesures efficaces pour gérer la consommation et les coûts liés à l’énergie », détaille Robin Cochard.
Pertinence et outils adaptés, clés d’un suivi intelligent des consommations
Sortie en 2011, la norme ISO 50 001 apporte la méthodologie pour la mise en place d’un système de management de l’énergie (SME) afin de garantir l’amélioration continue de la performance énergétique de son usine. Le suivi, la mesure et l’analyse des performances énergétique et sont des éléments clés. en d’autres terme, il s’agit de mettre en œuvre un sige.
Pour se traduire par des économies et une efficacité réelle, l’installation d’un système de gestion de l’énergie doit être le résultat d’une réelle stratégie de l’entreprise. « Rien ne sert de dépenser des milliers d’euros en instrumentation si personne n’est à même de gérer l’outil de gestion », estime Juliane Jundt.
L’analyse systémique, qui étudie la quantité d’énergie nécessaire à la fabrication du produit final, identifie les sources de récupération de chaleur fatale et définit les Indicateurs de Performance Energétique (IPE) à suivre, est un préalable recommandé par Actemium.
« En parallèle, nous pouvons réaliser un plan de comptage afin de définir les types de mesures à mettre en place et l’emplacement des capteurs sur site. Nous instrumentons ensuite la ligne, l’atelier ou l’usine selon le souhait de l’industriel » détaille Thierry Delpech, directeur du développement chez Actemium. En tant qu’intégrateur, Actemium propose le matériel et le système de gestion de l’énergie les plus adaptés aux besoins de l’entreprise et a également développé ses propres logiciels de gestion énergétique.
Efficacité énergétique, facteurs d’influence et Data Analytics
En plus d’apporter une aide à l’optimisation de la production, la mise en commun de l’ensemble de ces données permet de présenter à chaque personne de l’usine concernée celles qui l’intéressent spécifiquement
Via le suivi énergétique, l’industriel peut optimiser son process et la conduite des équipements par l’analyse de différents facteurs d’influence, ce qui impacte les consommations et la performance des équipements (météo, pic de production…). L’enjeu est désormais d’aller plus loin que la simple récolte de données énergétiques et identification des postes consommateurs. Actemium travaille par exemple avec un consortium de coopératives céréalières pour optimiser le fonctionnement des ventilations de refroidissement du grain et optimiser leurs dépenses énergétiques. « Les ventilateurs tournaient en permanence au maximum afin d’assurer le refroidissement, ce qui n’était pas optimal d’un point de vue énergétique. Après un audit et l’installation de capteurs, nous avons mis en place un système de collecte de données puis réalisé une phase de data analytics pour établir des règles métiers. Aujourd’hui, en fonction de divers paramètres extérieurs comme le type de grains, le volume stocké, la température extérieure… nous proposons à l’opérateur le mode de fonctionnement idéal du ventilateur », explique Thierry Delpech.
Rendre intelligente la donnée
Avec le big data, les données énergétiques sont traitées en temps réel et corrélées à d’autres (production, maintenance) afin d’ajuster et conduire les procédés de la manière la plus optimale. Le tout s’effectue en fonction des facteurs d’influence et peut donner le coût de fabrication d’un produit, en incluant son coût énergétique.
« En plus d’apporter une aide à l’optimisation de la production, la mise en commun de l’ensemble de ces données permet de présenter à chaque personne de l’usine concernée celles qui l’intéressent spécifiquement », ajoute Thierry Delpech. Soit un levier supplémentaire pour aller encore plus loin dans l’analyse de sa consommation énergétique.