Le robot industriel, l’outil qui réinvente l’usine
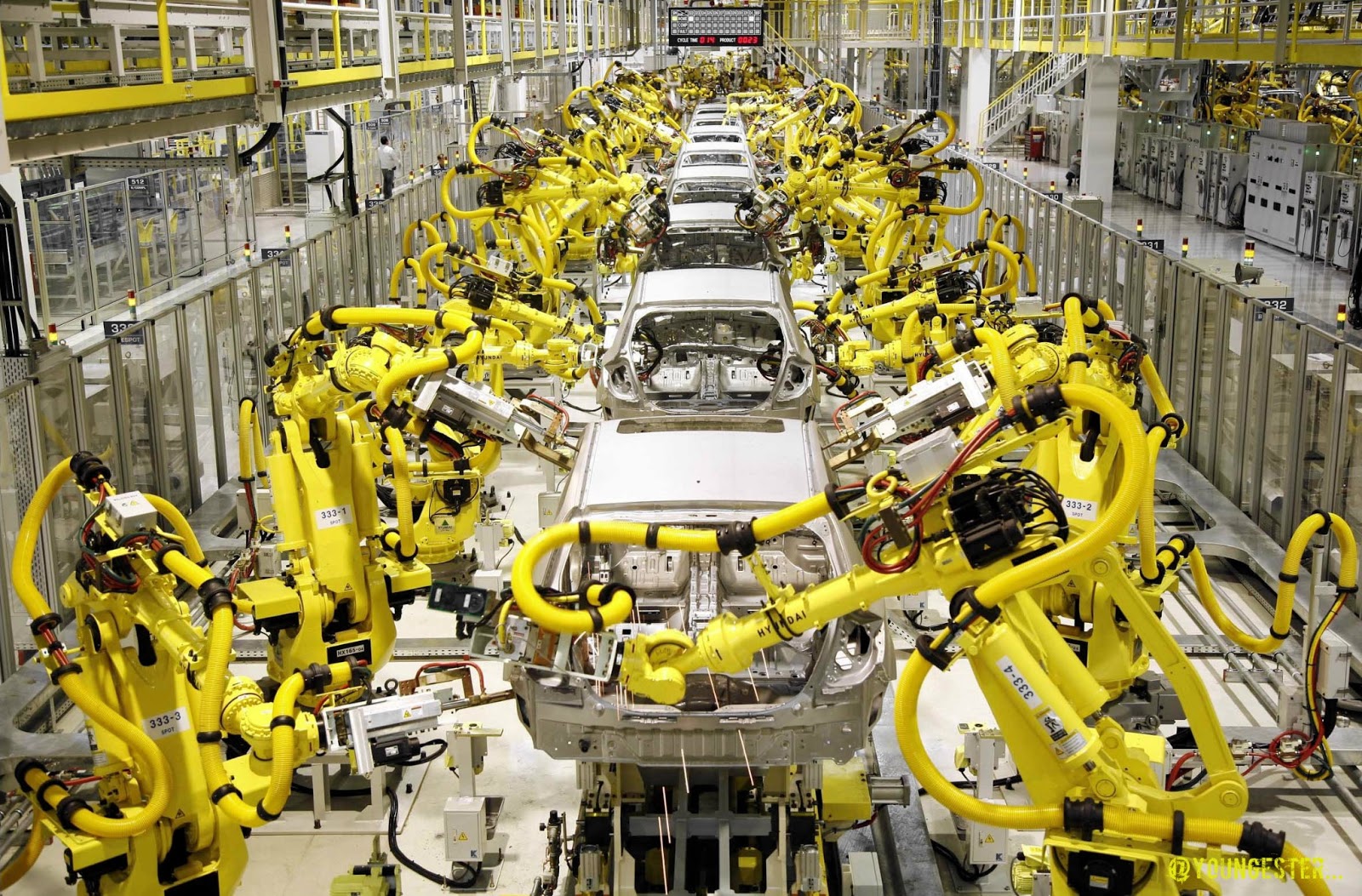
Les robots sont utilisés depuis longtemps dans l’industrie, à commencer par celle de l’automobile. Avec l’industrie du futur, une autre approche de la robotique est née, réinventant l’usine pour une industrie plus efficace et, contrairement aux idées reçues, plus humaine.
Outil phare ayant pris son essor pendant la troisième révolution industrielle, le robot permet l’automatisation de certaines tâches sur les lignes de production. Concrètement, il se présente sous la forme d’un bras articulé associé à une baie de commandes. Il est livré nu par le fabricant, c’est-à-dire sans effecteur (torche de soudure, caméra, pince…) qui définit le process qu’effectuera le robot.
Seul, il ne peut rien produire. Il doit donc être intégré dans une application industrielle, ce qui lui apportera sa valeur ajoutée. C’est là qu’entre en jeu l’intégrateur, comme Actemium. En plus de concevoir l’effecteur, il travaille sur les systèmes de protection et de sécurité autour du robot ainsi que sur les périphériques qui l’entourent, comme son système de déplacement. L’ensemble de ces éléments constitue une cellule robotique, livrée clés en main.
Robotiser l’industrie : pourquoi ça bloque ?
Certains pays sont à l’avant-garde de la robotisation : Allemagne, Japon, États-Unis… La France accuse en revanche un certain retard. Ses PME disposent donc d’un vrai potentiel de croissance et de développement par le biais de la robotisation. Parmi les points de blocage, un coût trop élevé et une mise en œuvre trop complexe sont souvent évoqués. En France, on compte ainsi 124 robots pour 10 000 salariés contre 273 pour l’Allemagne et 160 pour l’Italie.
Pour Jérémie Pedros, chef de l’entreprise Actemium Robotique et Automation, les risques, notamment financiers, sont pourtant moindres. « Comme le robot est un élément standard, s’en faire prêter un reste assez simple. Certains clients voulant industrialiser un procédé sont dans l’inconnu. Nous supprimons cette part d’inconnu en leur proposant un démonstrateur, un robot dont nous disposons dans notre atelier, pour tester et valider la performance de l’outil avant investissement ». Sans compter qu’une fois l’installation effectuée, « nous formons les opérateurs à l’utilisation des robots et nous accompagnons l’entreprise dans ces changements, jusqu’à la maintenance ».
Que peut-on robotiser dans l’industrie ?
Certaines tâches sont couramment robotisées, comme les opérations de fonderie, à risque pour les opérateurs ou la manutention de charges lourdes. Toutes ne s’y prêtent cependant pas : « L’idée est que l’homme soit le pilote. La mise en œuvre technologique a ses limites, notamment financières, et ce n’est pas pertinent de robotiser certaines tâches », précise Stéphane Vallette, chef de l’entreprise Actemium Maintenance Intégration.
Un robot industriel, pourquoi faire ?
En plus de l’évident gain de productivité associé à la robotisation, qui permet de produire plus efficacement en réduisant les coûts, la flexibilité est l’un des intérêts majeurs du robot. Par sa nature, il amène une capacité à évoluer, au contraire d’une machine spéciale : « elle est fabriquée pour correspondre parfaitement aux besoins du client, mais lorsqu’il y a des évolutions du produit, des contraintes, des cadences, de l’organisation, la machine spéciale est tellement spécifique à une application qu’elle est très difficile à faire évoluer, explique Jérémie Pedros. Avec le robot, c’est tout le contraire. Ses programmes et ses fonctionnalités peuvent être adaptés pour s’ajuster aux diverses évolutions. Un investissement sur un robot se fait à long terme ».
Les robots font peur car l’on croit qu’ils vont détruire des emplois. Or plus on robotise, moins on a de chômage car l’entreprise gagne en compétitivité, ce qui permet de ne pas délocaliser
Robotiser participe également à l’amélioration de la qualité des process et des produits : « on sait que le robot va répéter une tâche, toujours de la même manière, avec la même performance, la même vitesse, la même reproductibilité de mouvement » détaille Jérémie Pedros. Bénéfice sous-jacent ? Une qualité constante avec moins de rebuts et de retours.
« Robotcaliser » : plus de productivité pour ne pas délocaliser
Le terme « robotcaliser » a été inventé par le groupe Robotique du Symop. L’idée sous-jacente est de proposer la robotisation comme alternative à la délocalisation. L’automatisation de la production permet d’augmenter la productivité. « Les robots font peur car l’on croit qu’ils vont détruire des emplois. Or plus on robotise, moins on a de chômage car l’entreprise gagne en compétitivité, ce qui permet de ne pas délocaliser » explique Stéphane Vallette.
La robotisation serait même créatrice d’emploi. Historiquement, d’après une étude du cabinet Deloitte, la technologie a généré plus d’emplois qu’elle n’en a détruits. Les postes les plus rébarbatifs ou dangereux disparaissent au profit de nouveaux, comme la conduite de machines, la maintenance et l’entretien des robots.
Réinventer l’usine avec les robots et cobots, alliés de l’homme
« L’industrie 3.0 a eu tendance à beaucoup automatiser les procédés et fabrications, dans une approche de standardisation des produits. Elle est allée tellement loin dans la robotisation qu’elle a sorti l’homme de l’usine, explique Jérémie Pedros. L’industrie 4.0, ou industrie du futur se prête au contraire à une autre approche de la robotique, qui place l’homme au cœur de l’usine et lui permet de se réapproprier l’outil de production. »
En remplaçant ou assistant l’homme sur les postes à risques, pénibles ou générateurs de TMS (manutention de charges lourdes, risques d’émanations, environnement bruyant…), ils contribuent à réduire la pénibilité au travail permettant à l’homme de se concentrer sur des tâches à valeur ajoutée.
Évolution récente en robotique, les « cobots » s’inscrivent également dans cette idée. Le cobot aide et assiste l’homme, travaille en interaction avec lui, toujours sous le pilotage de l’opérateur. Autre atout, « la cobotique démocratise la robotique. Elle est plus simple à mettre en place, avec des coûts réduits, mais nécessite beaucoup plus d’études en amont afin de garantir la sécurité de l’installation » explique Stéphane Vallette. L’évolution vers la notion d’homme augmentée, avec un robot qui répond aux idées et à la pensée de l’homme, n’est qu’à quelques pas.