La 3D dans l’industrie, test virtuel avant expérience réelle
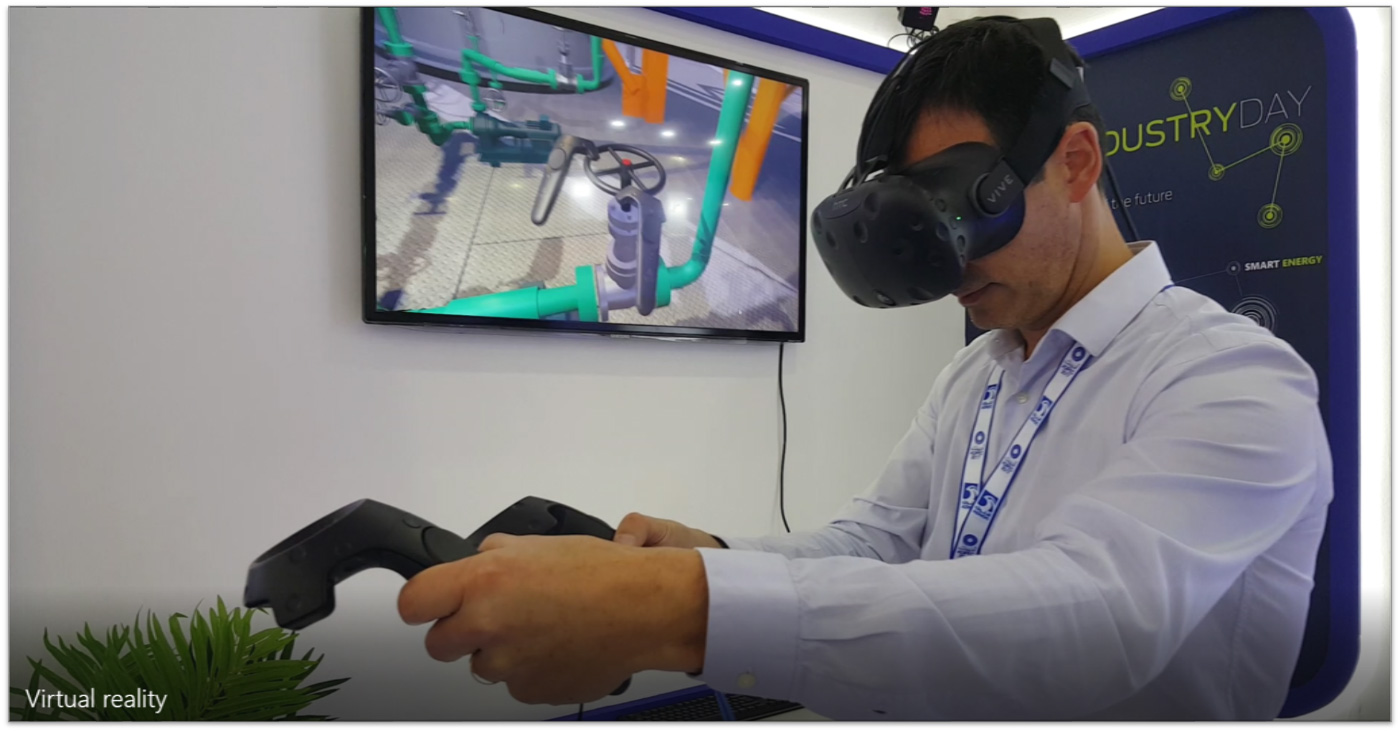
Qu’il s’agisse d’aider à la conception d’une installation, de faciliter la formation, de sécuriser un process ou tout simplement de gagner du temps, l’utilisation de la modélisation et simulation 3D dans l’industrie semble particulièrement prometteuse. Certaines applications ont d’ailleurs déjà fait leurs preuves.
Si l’aérospatiale, l’armée ou l’automobile ont été les premiers secteurs industriels à utiliser les technologies 3D, l’évolution de ces dernières et la démocratisation des outils graphiques permettent aujourd’hui à tous d’accéder à des techniques innovantes .
Les modélisation et simulation 3D face au secteur industriel
« Au vu de l’investissement de certains clients sur leur installation, pouvoir montrer ce qu’elle sera représente un gros avantage. L’industriel visualise l’ergonomie de l’installation et son environnement, peut former les opérateurs aux gammes d’opération ou les futurs opérateurs de maintenance », note Patrick Mariage, chef de l’entreprise Actemium Poissy. « À partir des études de conception que nous réalisons, nous recréons l’installation en 3D virtuelle, pour que le client la voie avec les opérateurs évoluant autour ».
À cette meilleure appréhension de certaines problématiques au sein d’une usine, ces techniques 3D ajoutent d’autres intérêts. « Nous exploitons au maximum la maquette de conception, auparavant utilisée uniquement sur l’étude. Grâce aux nouvelles technologies, nous la déclinons sous plusieurs formes, pour être adressée à différents types d’activités dans l’environnement industriel », détaille Paul-Eric Bertaud, 3D Innovation Project Manager chez Actemium.
Tester un process industriel ou une installation avec la 3D
Actemium est capable de simuler une installation en grandeur nature, dans un cadre réel et fonctionnel. « Nous avons réalisé une installation chez Solumat, un loueur de banches béton qui les remet en état à leur retour de chantier avant de les remettre en location. Son activité allait être multipliée par 3 et il cherchait une solution. Nous n’avions donc pas de cahier des charges et devions être force de proposition. Au vu de l’investissement, il fallait que l’on puisse lui montrer son installation avant réalisation ». L’entreprise a donc travaillé en ingénierie simultanée pour proposer des solutions techniques correspondant aux besoins et à l’investissement, tout en restant dans les logiques liées au personnel et au nombre d’opérateurs à conserver sur l’installation.
Modéliser l’installation avant de la réaliser concrètement contribue ainsi à éviter les incompréhensions : cadence, mauvaises données d’entrée, mauvaise interprétation du besoin final… Les opérateurs peuvent par ailleurs être intégrés dès le début du projet. « C’est une grave erreur de ne pas le faire, puisque ce sont eux qui vont adopter ou non une installation. Ils connaissent leurs métiers et les aménagements qui vont représenter une contrainte par rapport aux opérations à réaliser. Ils apportent leurs retours d’expérience sur ce que nous réalisons mécaniquement. », ajoute Patrick Mariage.
Créer un environnement en 3D dans lequel immerger les opérateurs
En capitalisant sur le modèle 3D utilisé pour concevoir la plateforme ou l’usine, il est possible de simuler un environnement et de le décliner pour d’autres utilisations, comme la formation. Actemium travaille sur des environnements difficiles d’accès et y a des contrats de maintenance qui impliquent une part de formations des opérateurs.
« Pour les plateformes pétrolières par exemple, les opérateurs, après leur formation initiale sont envoyés sur site pour une mise en situation. Or envoyer une équipe sur une plateforme présente énormément de contraintes liées à l’accessibilité du lieu, au coût et à la sécurité des personnes », commente Paul-Eric Bertaud. Les opérateurs doivent par ailleurs apprendre à travailler ensemble tout en n’étant parfois pas dans la même zone géographique, mais peuvent se retrouver à plusieurs dans un environnement virtuel.
L’idée est donc de rendre plus accessible et ludique la formation, notamment en utilisant la réalité virtuelle. « Les outils et technologies 3D dont nous disposons aujourd’hui sont issus du monde du jeu vidéo et déclinés dans le monde industriel. Nous reconstituons la plateforme, le jumeau numérique du bateau (FPU/FPSO) et y identifions les différents types d’activités liées à la formation. La maquette est ensuite déclinée en fonction de ces métiers ». Cette technologie permet de simuler un futur environnement de travail simplement et à moindre coût, de sensibiliser l’opérateur et de lui permettre de se former à sa vitesse.
La simulation 3D pour faciliter la compréhension des règles de sécurité
« Un dessin vaut toujours mieux qu’un grand discours pour sensibiliser à la sécurité ! », lance Paul-Eric Bertaud. Actemium peut décliner la modélisation 3D pour un scénario de sécurité en créant un environnement dans lequel la personne va se retrouver face à des situations de danger et de problèmes à résoudre.
« Chacun ne comprendra pas nécessairement une consigne de la même manière, différentes nationalités doivent être sensibilisées… Simuler un environnement virtuel dans lequel elles vont se projeter fait comprendre beaucoup plus rapidement les points d’attention à avoir tout en permettant de s’approprier le lieu ».
Simplifier les opérations de maintenance dans les milieux à risques
Certains secteurs comme le nucléaire impliquent d’envoyer des opérateurs de maintenance dans des zones contaminées. « Tout ne peut pas être effectué par des robots », estime Paul-Eric Bertaud. « L’idée est d’utiliser les modélisations 3D pour préparer de manière plus poussée les opérations en amont et ainsi diminuer le temps passé en zone contaminée. Démonter une pompe en atelier par exemple, c’est simple mais sur site, elle peut être difficile d’accès, entourée d’équipements sous pression… ».
Nous expérimentons au fil de l’eau et de l’avancée de la technologie par rapport à nos problématiques métiers
Dans le cas d’arrêts de tranche, même si le planning des opérations est étudié, plusieurs corps de métier intervenant en même temps peuvent se gêner. Simuler ces opérations de maintenance à grande échelle permet de vérifier que le processus établi est valable dans l’exécution réelle des opérations ».
Actemium et CEM Nucléaire (entreprise de VINCI Energies) ont également développé une solution de réalité virtuelle collaborative dédiée à la conception de projets.
Sur des environnements inaccessibles au public au vu des hauts niveaux de sécurité, la modélisation 3D permet enfin à des clients de visiter et d’être sensibilisés aux métiers et savoir-faire d’Actemium.
« Nous expérimentons au fil de l’eau et de l’avancée de la technologie par rapport à nos problématiques métiers », conclut Paul-Eric Bertaud. En permettant d’améliorer les conditions de travail des collaborateurs et de faciliter la conception d’installation, les nouvelles technologies se mettent au service de l’opérateur, du client et facilitent le travail du concepteur.