CND : des méthodes en constante évolution
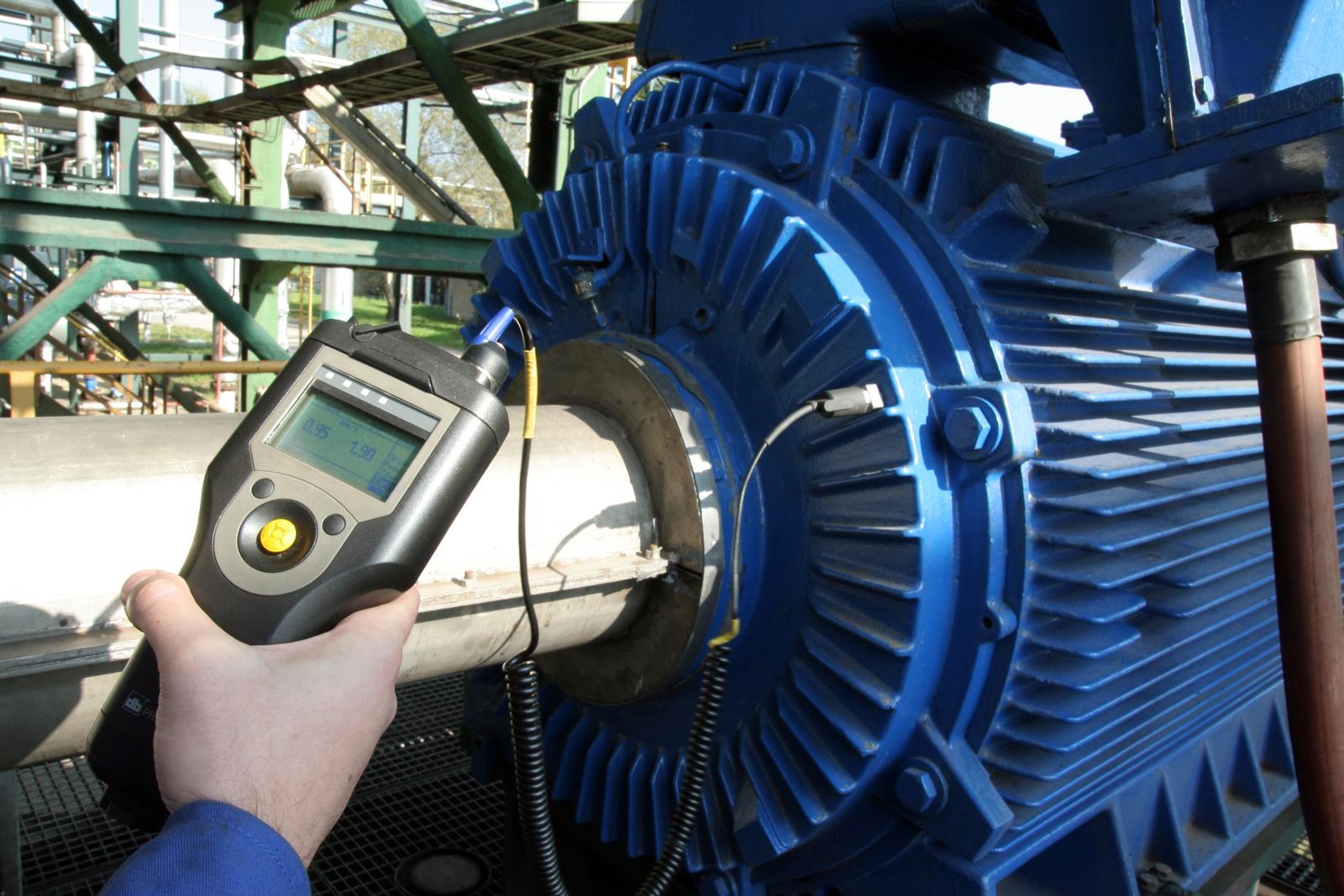
Le Contrôle Non Destructif (CND) permet de vérifier l’intégrité de pièces, composants, matériaux ou équipements sans les détériorer. Si les méthodes ne sont pas nouvelles, elles évoluent au fil des avancées technologiques.
Le Contrôle Non Destructif (CND) permet de « détecter des indications pouvant affecter le bon fonctionnement de l’installation ou de l’organe testé, qu’elles soient liées à la fabrication ou à son utilisation (fissures de fatigue), mais aussi les défauts d’aspect (corrosion, piqûre) ou des corps étrangers », explique Serge Selles, chef d’entreprise chez Actemium NDT Engineering & Services.
Au siècle dernier, « les premiers CND consistaient tout simplement à taper sur une pièce avec un marteau pour vérifier la constance du son sur toute la surface (un son creux indiquant un problème), ou à utiliser de la poudre de craie et de l’huile pour les premiers tests par ressuage, » s’amuse Serge Selles. Depuis, les méthodes ont évidemment évolué, au fil des avancées technologiques.
Les tests d’étanchéité, les ultrasons ou l’émission acoustique entre autres ont ainsi progressé en même temps que les équipements et les logiciels de traitement, tout comme les courants de Foucault et les ultrasons avec l‘évolution des sondes et capteurs de mesures. La radiographie est quant à elle de plus en plus remplacée par la radiographie numérique pour éviter les déchets liés à l’utilisation de films argentiques, ou par des contrôles à ultrasons car les limites de sensibilités évoluent…
Des méthodes aux multiples applications
Les méthodes utilisées dépendent du type et de la nature des composants ou structures à analyser et peuvent parfois être associées entre elles. Parmi ces différentes techniques, radiologie, ultrasons, ressuage, étanchéité, courants de Foucault, émission acoustique ou encore magnétoscopie sont les plus couramment utilisées.
Pour le secteur de l’aéronautique, nous inspections par exemple les moteurs d’avions pendant le cycle de production afin de garantir leur intégrité, ceci en utilisant l’UT en immersion, la radiographie numérique et les courants de Foucault.
Les entreprises utilisant le CND pour vérifier leurs produits appartiennent à des secteurs très diversifiés. Il s’agit principalement d’industries sensibles, produisant des composants au coût élevé ou dont la fiabilité est critique au niveau de la sécurité. Au-delà du secteur, les éléments à analyser varient, comme l’explique Serge Selles : « Au cours de ma carrière, j’ai été amené à tester l’étanchéité d’emballages de café, de boîtes de conserve pour chats, à faire des radiographies sur les premières roues de TGV… Nous avons également effectué une radiographie d’un sarcophage avant qu’il ne soit ouvert pour voir ce qu’il contenait ! ».
Améliorer la performance industrielle et la fiabilité
L’objectif premier des CND, répondre aux impératifs de sécurité, gestion des risques et qualité, s’applique à chaque étape du cycle de vie d’une pièce (fabrication ou exploitation). « Nous avons effectué des tests hélium par reniflage direct sur un méthanier pendant 5 mois afin de vérifier son étanchéité. L’arrêt technique était une première mondiale car la membrane primaire allait être totalement remplacée. Nous avons utilisé nos robots de contrôle, qui servent normalement durant la construction d’un méthanier. Le résultat final fut très concluant pour l’armateur. À ce jour le navire navigue sans aucun souci. »
Ces tests permettent également de surveiller le vieillissement des équipements et contribuent à prévenir les pannes. Utiliser les courants de Foucault sur des échangeurs permet par exemple de mesurer l’usure des tubes et de les boucher avant rupture.
« Depuis un an, nous intervenons sur un site d’EDF pour effectuer une assistance et expertise technique durant des tests hélium tranche en marche. Ils permettent de contrôler un équipement sans arrêter la production, ce qui représente un gain de coût, évite le démontage des pièces et le risque de créer des dégâts », explique Serge Selles.
La technologie avance, le CND également
Depuis le test au son, le CND a fait du chemin : contrôle visuel, puis gaz, traceurs, et maintenant capteurs. Présents dans toute l’industrie du futur et en particulier dans la maintenance, ces derniers, miniaturisés, sont plus rapides, plus précis et détectent des défauts de plus en plus petits. Autre amélioration : le contrôle par ultrasons peut s’effectuer sans fil, via le Bluetooth, et en utilisant un smartphone ou une tablette. La tomographie à rayons X, issue du domaine médical, permet d’obtenir une représentation en coupe ou en 3D de l’intérieur d’un objet. « Les appareils sont plus sensibles, permettent de détecter des éléments qui étaient invisibles auparavant, des méthodes plus performantes en remplacent d’autres, comme la radiographie par les ultrasons. Elles évoluent, sont complémentaires les unes aux autres », estime Serge Selles.
Nous avons maintenant la possibilité de placer 2 capteurs différents en un, par exemple pour utiliser les courants de Foucault avec l’ultrason, ce qui permet d’identifier des défauts à la fois surfaciques et volumiques – complète Brigitte Urbaniak. Dans le cadre d’une mission de maintenance, nous avons par exemple contrôlé le compresseur haute pression du moteur general électric 90 grâce à un équipement spécialement conçu pour recevoir cette pièce en contrôle par courant de Foucault et ultrasons.
Malgré une amélioration des logiciels de traitement et une meilleure sensibilité des appareils, « nous aurons toujours besoin de l’expertise et de la décision finale de l’homme. Même si une partie des contrôles est automatisée avec des seuils d’alarmes en production, le verdict final sera pris par le technicien CND », conclut le chef d’entreprise.